Foam Extrusion System
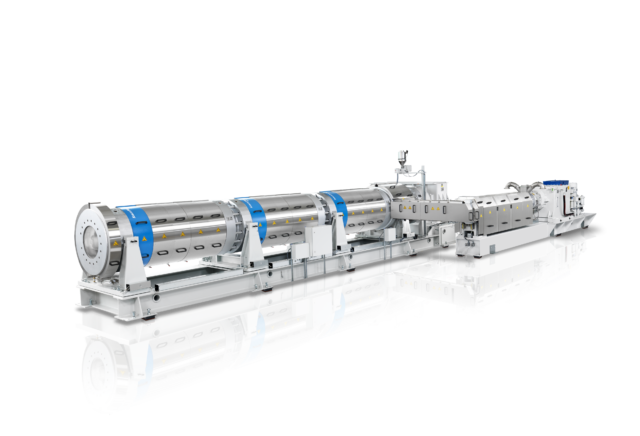
A co-rotating twin-screw extruder is used in the first stage so that the gas could be evenly dispersed in the melting elastomer.
This is used for manufacturing for building material of heat insulating boards, foam beads, Soundproof sheets, packaging materials, food trays, etc.
Product Features
It features a two-stage structure consisting of plasticization/gas injection stage and cooling stage. Adopting environmentally friendly physical foaming, it is a line that can handle from PS, PE and PP to heat resistant polymers of PET, PEI and PES.
The Schaumtandex ZE/KE type line, which consists of a twin-screw extruder for mixing and a single-screw extruder for cooling, improves foaming efficiency.
The cylinder and screw components of the twin-screw extruder are modularized, and high-quality products are possible to produce depending on the application by providing the optimum combination of transfer elements, mixing elements (or kneading elements), blister elements, returning elements, etc.
All cylinders for the foaming process are airtight so that the foaming agent is injected from the spacer ring. The cylinder in the processing section can be selected from L/D = 4D or L/D = 6D according to the individual foaming process.
The following optional cylinders are also available.
- Open type and closed type cylinders
- Side feed cylinder (L/D = 4D and L/D = 6D)
The Schaumtandex extruder is equipped with a patented ASD type special seal which has established a reliable new standard on sealing of the plastic processing at the side of gear box.
This special seal structure is effective because stable operating conditions are required for liquid or gas foaming agents and sensitive foaming processes with high pressure in line.
A water-cooled liner with a spiral groove is used for the feed section so that pellets of various sizes could be fed without problems.Therefore, a stable feed is secured in the entire operating area.
This equipment is effective for the production of the following foam sheets.
- Packing materials for food and home appliances.
- Foam construction material for heat insulation to absorb shock and sound.
- Industrial products such as seals, end protection stops and cover seals.
- Roof lining, seals, armrests and impact resistant products for the automobile industry.
- Large-capacity processing with a maximum of 1,500kg/h is possible by combining line configurations.
Processing capacity varies depending on the degree of foaming, resin material, product size and foaming agent.