About usCOMPANY
MISSION
Mission
Creative Driving Force to
Swell New Age Wave
Since our foundation in Tokyo Shinagawa in 1930, we have been providing rubber extruders and plastic extruders with a system including line devices accompanied to meet various requirements such as rationalization, labor saving and high quality demanding by our customers with motto of “Forming customer needs”.
As a result of aggressively advancing capital investment for the future such as state-of-the-art NC machines and inspection equipment, management systems, test facilities etc. under any severe circumstances, many consultations and instructions from top Japanese manufacturers in various fields have been approaching to us.
We will continue to strive to provide products and services that satisfy our customers both domestically and abroad without for getting our ambitions at the time of their founding and will work together to make a long term partner relationship so that our customers and our manufacturers can develop each other. We sincerely appreciated for your guidance and acceptance.
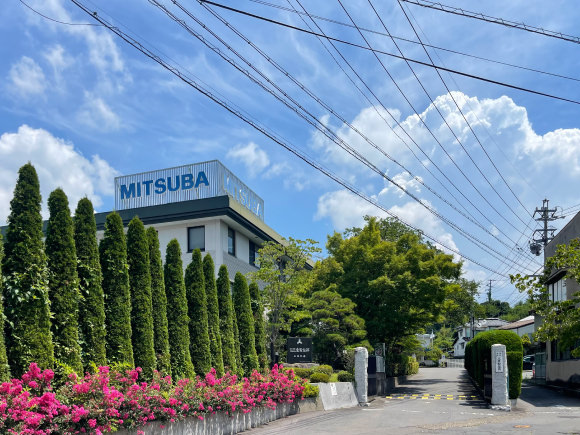
OVERVIEW
Overview
- Corporate Name
- MITSUBA MFG. CO., LTD.
- Foundation
- On April 20, 1930
- Scope of Business
- Manufacturing and marketing of EXTRUDERS FOR RUBBER & PLASTICS and WIRE COATING MACHINES
- Other services related to the above-cited business.
- Capital
- 50,000,000yen
- Location
- Head Office / Koyama 5-1-1, Shinagawa-ku, Tokyo, Japan 142-0062 Telephone +81+3-3711-5101 / Facsimile +81+3-3711-5109
Ueda Factory / Chuo-higashi 5-14, Ueda-city, Nagano, Japan 386-8638 Telephone +81+268-24-3131 / Facsimile +81+268-24-3136 - Officer
- President KENICHI HORIUCHI
- Banks of account
- The Hachijuni Bank, Ltd. Uedahigashi branch / Sumitomo Mitsui Banking Corporation. Ueda Branch / THE NAGANO-KEN SHINKUMI BANK. Ueda Branch / MUFG Bank, Ltd. Meguro-Ekimae Branch / The Shoko Chukin Bank, Ltd. Fukagawa branch
- Membership of professional institutions
- The Society of Rubber Science and Technology, Japan / Japan Plastics Machinery Association / Japan Society of Plastics Technology / Japan Society of Polymer Processing
- ISO9001
- Acquired ISO9001 (2015 version), an international standard for quality control, in all product fields.
HISTORY
History
- 1930
- MITSUBA MFG. CO.,LTD. Started operation at Koyama,Shinagawa-ku,Tokyo and initiated manufacturing of auxiliary machines to befitted to rubber extruders.
- 1931
- A rubber extruder of its own was completed.
- 1939
- Designated as a navy-controlled factory and went into volume production of arc welding machine and spot welding machine.
- 1945
- Temporary operating foothold was built up immediately upon destruction of its factories and production facilities by war damage. Another production facilities were Newly built in Ueda-city and started operation.
- 1949
- Reconstructed Tokyo factory resumed its operation.
- 1950
- Resistance welders’ manufacturing come into service.
- 1951
- A plastics extruder of its own was compled.
- 1955
- D.C. arc welding machine and argon arc welding machine were developed.
- 1960
- Head office building was newly built.The 1st extension work was added to the Ueda factory.
- 1963
- Automatic chain making line and automatic mesh making line were completed.
- 1965
- The head office building and the Tokyo factory were enlarged. The 2nd extension work was added to the Ueda factory as well.
- 1973
- Twin screw vent type rubber extruder and atmosphere vulcanizing rubber wire coating machine were completed. “Invention & Service Test Subsidy” was granted by the Science and Technology Agency.
- 1975
- Single screw vent type rubber extruder manufacturing was initiated upon finalizing a technological tie-up with HERMANNBERSTORFF in West Germany.
Tokyo factory was transferred and consolidated into Ueda factory for the purpose of production efficiency and technological innovation. - 1983
- Exterior sheath continuous vulcanizing line with the aid of mechanical heating of two-layer rubber hose was developed.
“Technology Development Subsidy” was granted by the Ministry of International Trade and Industry. - 1985
- Expand production capacity by expanding the Ueda factory and introducing various NC machine tools
- 1987
- Renovation of the head office and start of computer introduction to the engineering department and production management department
- 1988
- Introduction of new machine tools at Ueda Factory
- 1989
- Ueda factory : Newly constructed Administration development building,Canning factory, Processing parts controling building and Automatic warehouse building. Implemented environmental completion and greening in permises.
- 1990
- Introduced five-sided processing machine with other new machines as well as production management system and CAD system Production management system,CAD system introduced.
- 1991
- Introduced laser processing machines, wire electric discharge processing machines, etc.
Improved the precision processing capacity of major parts as well as production capacity by enlargement of the assembiy plant. - 1992
- The capital increased to 50 million yen.
Technology partnership in pintype extruder with Berstorff GmbH. - 1993
- Technology partnership in pin-convert-type extruder with Berstorff GmbH.
- 1998
- Speed up operations at Ueda Factory by establishing network system and updating CAD.
Introduced and implemented a new personnel and treatment system - 2000
- Acquisition of ISO9001 certificate.
- 2001
- Introduced new machines such as complexed lathes and NC lathes as well as viscosity measuring machines for in-house production and quality improvement.
The new headquarter office building was built at 5-1-1 Koyama, Shinagawa-ku, Tokyo.
Received the fourth courtesy letter from the Tokyo Metropolitan Tax Bureau as a good tax return corporation, following 1986, 1991, and 1996. - 2002
- Acquisition of ISO9001:2000 certificate.
- 2003
- Ueda factory: Work environmental improvement.
- 2004
- Latest advanced machines in complex processing, 5-axis machining center, NC horizontal boring to expand production capacity.
Technology partnership in gear pump with Berstorff Inc.
Technology partnership in colgated forming & Sales collaboration in plastic net forming line with Corelco company. - 2005
- With introduction of NC lathe, Wire-cut electric discharge processing machine and general-purposed super-high-speed small hole electrical discharge processing machine, the ability in the precise processing was improved.
Hold a ceremony and celebration to commemorate the 75th anniversary of the company’s founding. - 2006
- Introduction of horizontal machining center.
- 2007
- Introduced the integrated document management system & implemented electronic design drawing in conjunction with CAD systems to improve the efficiency in design as well as in operation of drawing release.
GHP typed air conditioning equipments were installed in all plants for the energy saving and improvement of working environment. - 2008
- With the introduction of a cylindrical grinder for long (4,000mm)length, processing ability of extruder screw was improved.
- 2009
- Signed the sole agency agreement in Japan with KlausMaffei Berstorff, (KMB).
Acquisition of ISO9001:2008 certificate. - 2010
- By introducing SFA (Sales Force Automation system), achieved internal sharing of mutual information & in deepening understanding.
- 2011
- With the introduction of large-scale NC front lathe, enhanced in-house processing ratio of large components manufacturing.
- 2013
- Introduced TOC project management system by Avraham Y Goldratt Institute (AGI) Inc.,
Newly established two of the latest advanced horizontal machining centers and enhanced the ability in precised processing manufacture.
Signed an agency agreement with THE Machines Yvonand SA.
Contributing to orders for 4 sets of tire manufacturing full line as a Japanese distributor of Krauss Maffei Bersterff. - 2014
- Updated CAD, CAM and NC machine simulation software.
- 2015
- Received a subsidy as Strategic basic technology advancement support project by the Ministry of Economy, Trade and Industry (Sapoin). In collaboration with Kanazawa Institute of Technology, started development of wire coating technology using supercritical foaming technology.
Received an Award of “NAGANO Manufacturing Excellence 2015”. - 2018
- Signed an agency agreement contract with CJTEK Co., Ltd.
Received the Labor Bureau Director’s Encouragement Award for Safety and Health from the Nagano Labor Bureau. - 2020
- Recognized as a “Regional Future Leading Company” by the Ministry of Economy, Trade and Industry.
- 2022
- New production control system begins operation.
Registered as a Nagano Prefecture SDGs Promotion Company.
BUSINESS SITES
Business Sites
Head Office
Koyama 5-1-1, Shinagawa-ku, Tokyo, Japan 142-0062
Telephone +81+3-3711-5101 / Facsimile +81+3-3711-5109
The third “Nishikoyama” get off, a 5-minute walk Tokyu Meguro Line from Yamanote Line Meguro Station.
Ueda Factory
Chuo-higashi 5-14, Ueda-city, Nagano, Japan 386-8638
Telephone +81+268-24-3131 / Facsimile +81+268-24-3136
About 5 minutes by car from the Joushin’etsu Expressway “Ueda Sugadaira interchange”
Hokuriku Shinkansen “Ueda station” get off, about 10 minutes by car.
HEALTH and SAFETY
Health and Safety
Ⅰ Works for safety and health
Based on the recognition that the physical and mental health of each employee is the basis of sound business management, Mitsuba MFG Co., Ltd. promotes safety and health activities with the participation of all employees toward the realization of a “comfortable workplace where employees could work safely and safely”. In addition, we are working on safety and health activities to maintain and improve the working environment for realization of a “zero accident” workplace.
Ⅱ Safety and Health Code in Conduct
- Compliance with the law
Comply with legal requirements, including laws, regulations and notifications related to occupational health and safety. - Investment of management resources.
Mitsuba MFG Co. Ltd. will invest human, technical, and financial management resources to realize a safe and healthy workplace both physically and mentally. - Eliminate/reduce dangerous/harmful factors.
Carry out risk assessment, identify dangerous/harmful factors, make improvements, and eliminate/recommend the method/proposals. - Education / training
Establish an education and training system for safety and health to improve the qualifications of all employees
MITSUBA MFG. CO., LTD.
President and CEO Kenichi Horiuchi
Ⅲ Safety patrol
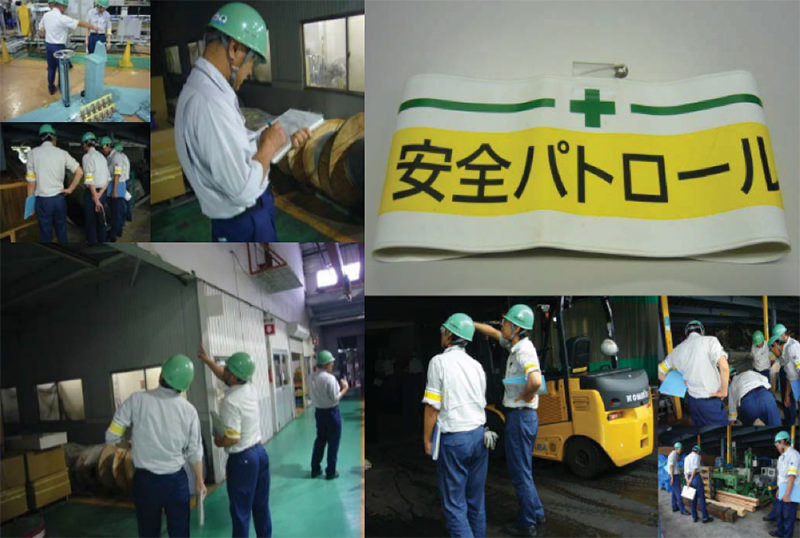
A safety patrol is carried out every month by the “Safety and Health Committee” organized by the representatives of each department, with the officer in charge at the top. It strictly checks the safety environment of factories and surrounding facilities, and functions as a starting point for PDCA for
Ⅳ 5S Initiatives
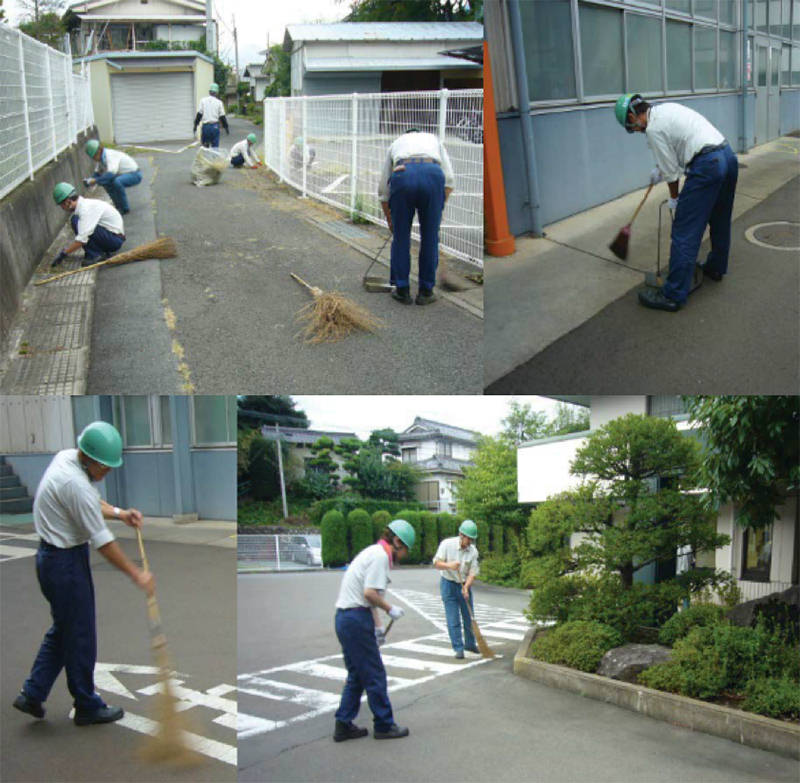
We have set up the “Environmental Improvement Promotion Committee” to consider the environmental improvement of each department and carry out a campaign to develop it into specific environmental improvement activities. In addition to this, we spend business hours every other week by everyone to work on cleaning, to organize and tidy up the entire company.
Ⅴ Works for mental health

With the implementation of the “stress check”enacted in 2015, we have established a system for stress check in partnership with an external consultant to develop counseling and introduction of medical institutions mechanism. We distribute the “Mental Health Handbook” to all employees to make the system known.